Contact Us
+8618700875368
No.6 Zhangba First Street, High-Tech Area, Xi'an City, Shaanxi Province, P.R. China 710065
SO2 gas corrosion testing for Coatings
2023-11-23 11:37:14
What is SO2 gas corrosion testing?
SO2 gas corrosion testing is a crucial process to evaluate the corrosion resistance of materials and coatings in the presence of sulfur dioxide gas. This type of testing is particularly important in industries such as oil and gas, chemical, and power generation, where materials are exposed to SO2 gas and need to withstand its corrosive effects. In this article, we will discuss the significance of SO2 gas corrosion testing and the use of SO2 gas corrosion chambers in conducting such tests.
Importance of SO2 Gas Corrosion Testing:
Sulfur dioxide (SO2) is a highly reactive gas that can cause severe corrosion in various materials. It is produced during the combustion of fossil fuels containing sulfur impurities, such as coal and oil. When released into the atmosphere, SO2 can react with moisture to form sulfuric acid, which is a strong corrosive agent. This acid can corrode metals, concrete, and other materials, leading to structural damage and equipment failures.
SO2 gas corrosion testing helps in determining the resistance of materials and coatings to the corrosive effects of SO2 gas. By subjecting test specimens to controlled environments simulating SO2 exposure, researchers can evaluate the performance and durability of materials in real-world conditions. This testing is essential for selecting suitable materials for construction and manufacturing processes, ensuring the longevity and reliability of structures and equipment.
SO2 Gas Corrosion Chambers:
LIB SO2 gas corrosion chambers are specially designed enclosures that simulate the corrosive environment caused by exposure to SO2 gas. These noxious gas chambers provide a controlled atmosphere where test specimens can be exposed to predetermined levels of SO2 gas concentration, temperature, and humidity. The chambers are equipped with monitoring and control systems to ensure precise testing conditions.
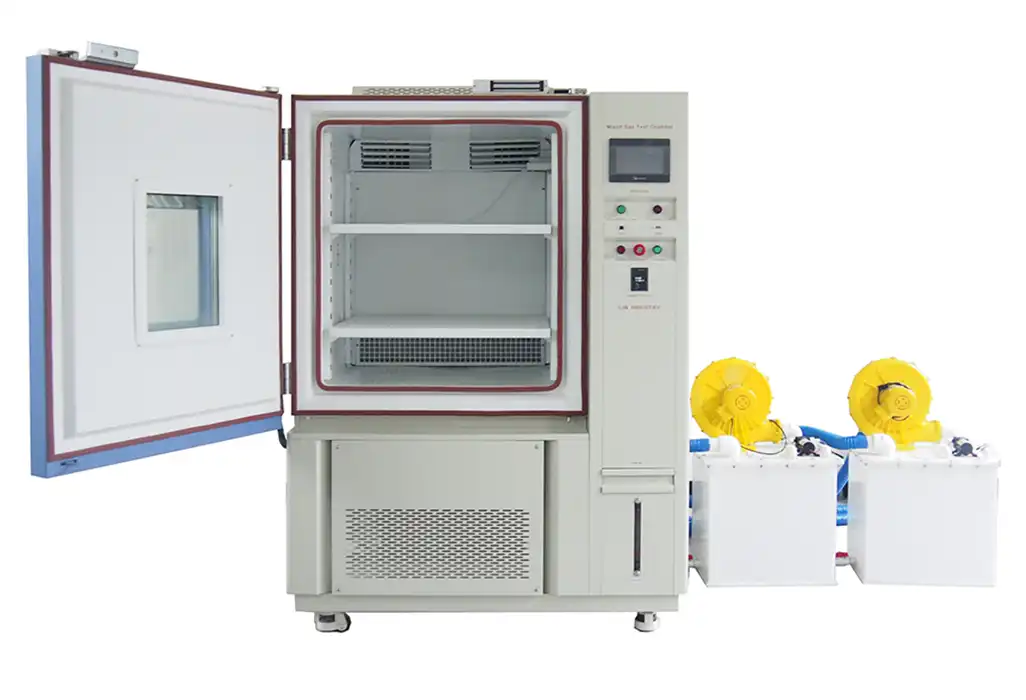
Model: LIB SO-225
Internal Dimensions (mm): 500*600*750
Overall Dimensions (mm): 960*1150*1860
Temperature Range: 15 ℃ ~ 80 ℃
Temperature Fluctuation: ± 0.5 ℃
Temperature Deviation: ± 2.0 ℃
Humidity Range: 30% ~ 98% RH
Humidity Deviation: ±1% RH
SO2 Concentration: 25±5 ppm
Air Change Rate: 3~5 /h
During the testing process, specimens are placed inside the SO2 gas corrosion chamber, and the chamber is sealed to prevent any leakage. SO2 gas is then introduced into the chamber at the desired concentration, typically ranging from a few parts per million (ppm) to several hundred ppm. The temperature and humidity levels can also be adjusted to simulate different environmental conditions.
The test duration can vary depending on the specific requirements and industry standards. Typically, specimens are exposed to SO2 gas for a specific period, ranging from a few hours to several weeks. During this time, the specimens are periodically inspected to assess any signs of corrosion, such as surface degradation, color changes, or weight loss.
LIB SO2 gas corrosion chamber SO-225 is good for this test. Kindly contact us to get more information.
Send us a message
Please Leave your Message Here! We Will Send Detail Techincal Brochure and Quotation to you!